
Re-inventing the future of mining through purpose-built technology solutions
We thrive at the intersection of operational imperatives and technological solutions
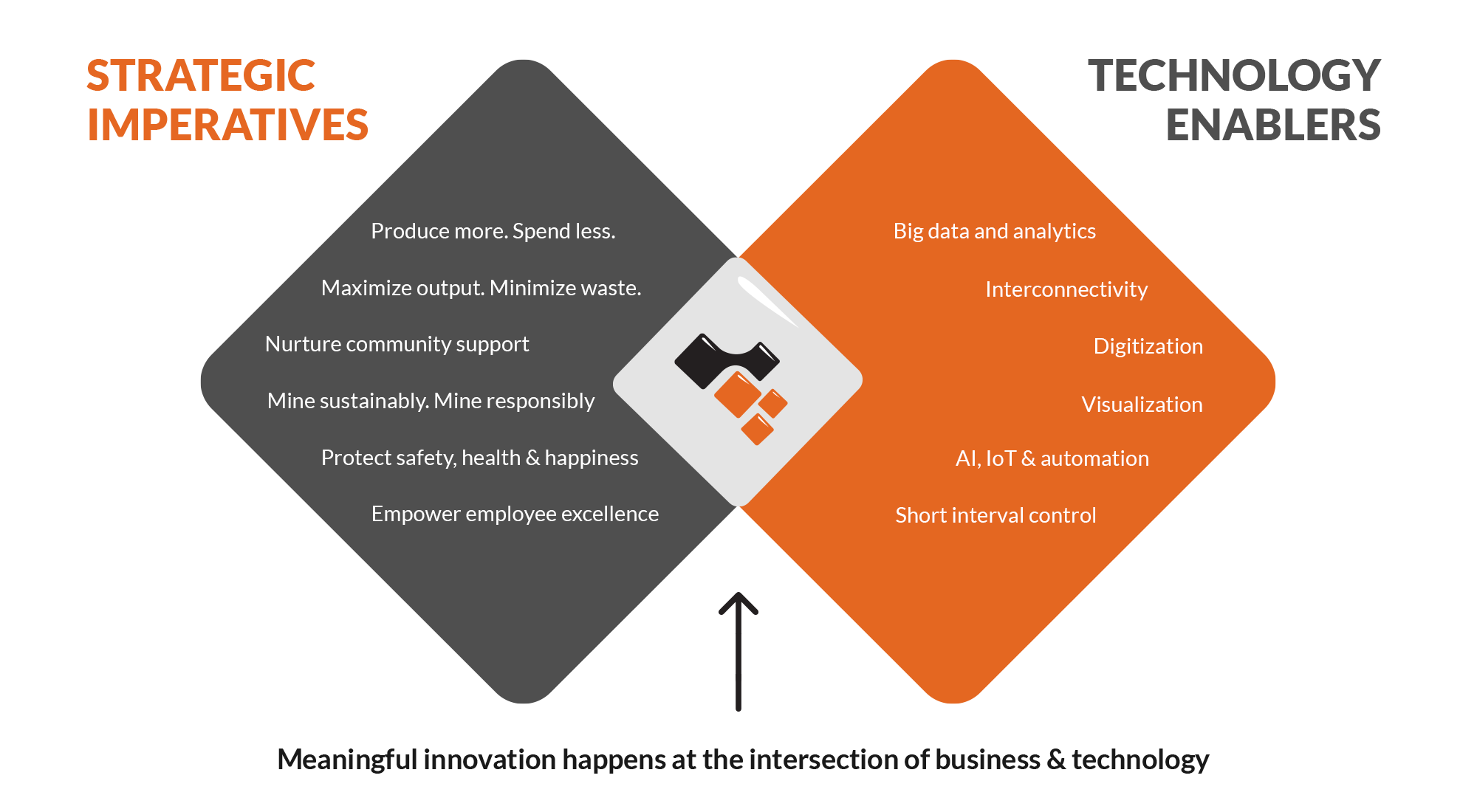
1 Advise
2 Execute
3 Optimize
Monitor, Manage & Optimize Anything That Matters
… In Real Time
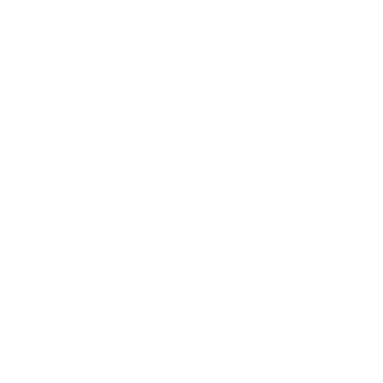
Be Informed
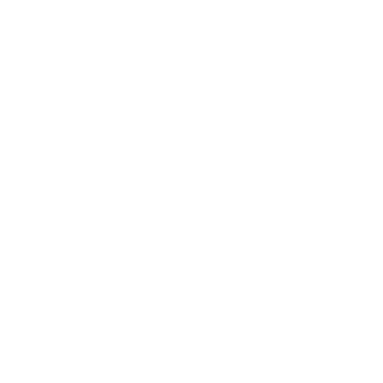
Eliminate Costs
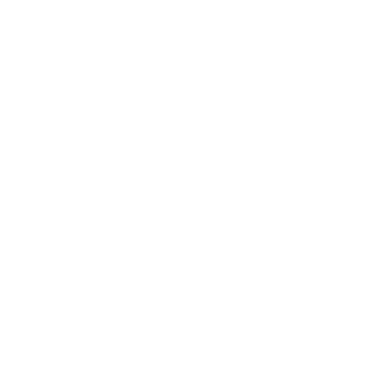
Exceed Production Targets
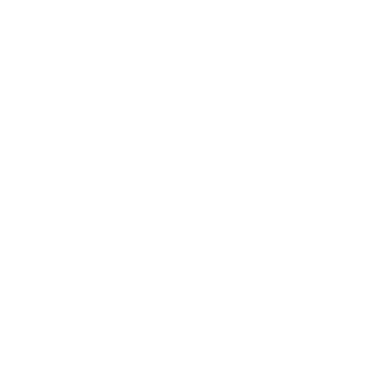
Empower Your Workforce
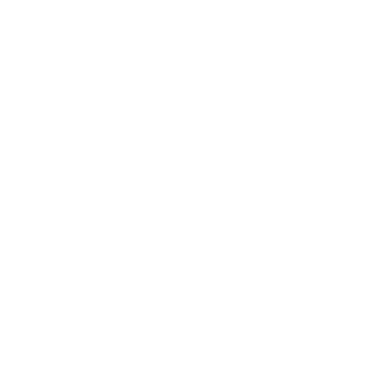
Save Lives
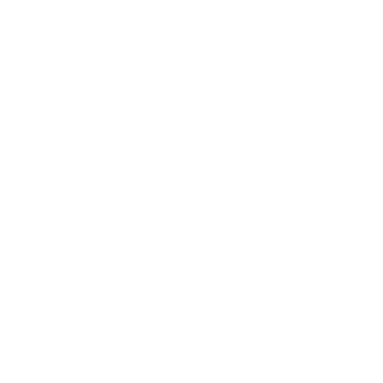
Stay Connected
Delivering guaranteed results
throughout the entire technology value chain
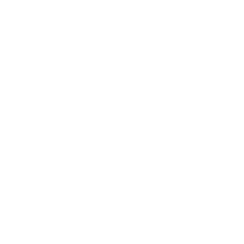
Specialized Advisory Services
Technology strategy and roadmap development
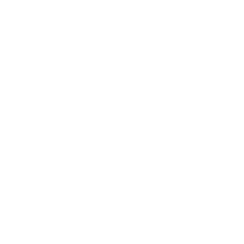
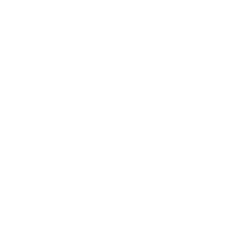
Execution Excellence
Best-of-breed solution design and technology sourcing
Solution implementation and integration services
Ongoing technical support, including on-site services
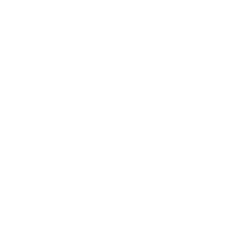
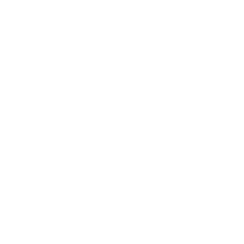
Operational Optimization
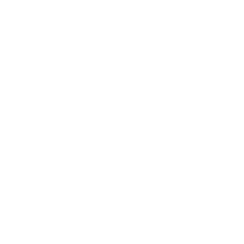
Solutions-driven
Technology.
RAMJACK is different. We’re technology agnostic so all our projects start with solving the problem first and only then are the right technologies sourced, integrated and optimized.”
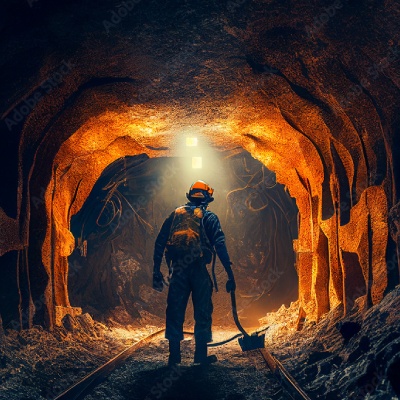
Underground
Ramjack’s underground mining technologies guarantee increased production and safety improvements by monitoring, managing, and optimizing your assets: people, processes, equipment, and the rugged environment in which you operate.
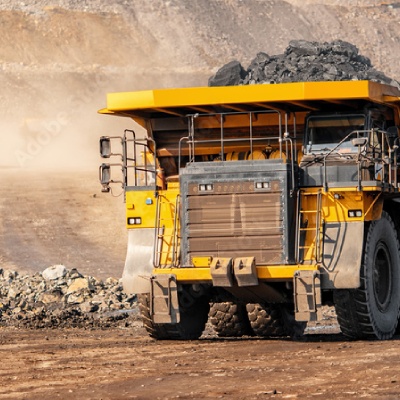
Open Pit
Our surface mining solutions optimize safety and productivity through groundbreaking advances in real-time information management combined with the expertise and technology access to integrate the ideal, purpose-built solution.

Services & Support
Our mining services ensure real value generation from your operational technology, and can include technology ‘needs’ assessments, roadmap generation, implementation, and training, up to and including full operations of your systems via our Remote Operation Center,.
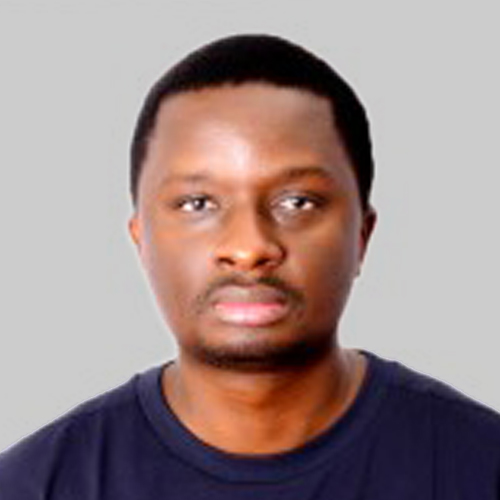
Kofi Appiah-Dwomoh
West Africa

Rupert Birch
Europe | Middle East | North Africa
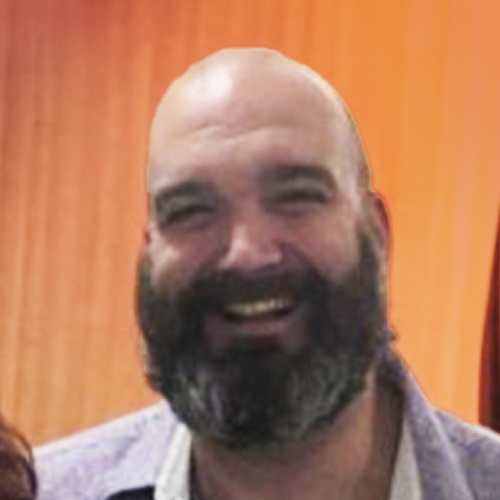
Stephane Cantin
Central America | South America
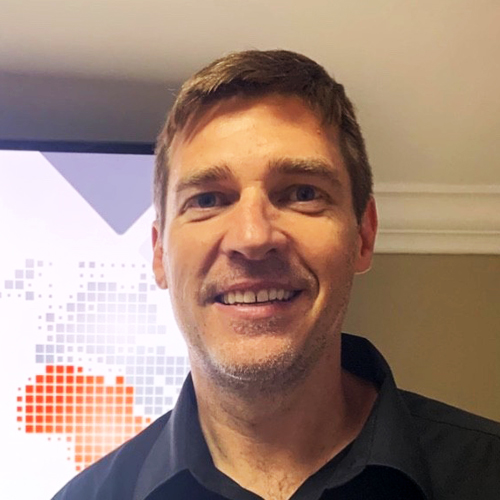
Mike Jackson
Sub-Saharan Africa | Asia Pacific |
North America
We guarantee increased value from your existing technology systems, with full ROI on our advisory and integration services, within one budget cycle.
With a full product suite and service offering we can help improve safety, productivity and effectiveness at your mine today.